微細加工
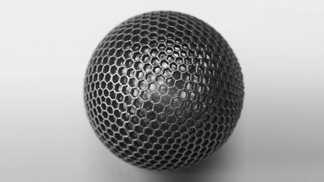
加工時間の短縮、高い動的性能、高精度での加工を実現
微細加工には、穴あけ、彫刻、構造化、切断など様々な加工を含み、多くの場合、非常に高い精度とスピードが求められます。ガルバノスキャナ―用いたレーザー加工は、複雑なパターンや構造を処理する上で柔軟性と動的性の点で他の方法より優れています。
加工可能な素材は、プラスチックからガラス、セラミック、そして金属に至るまで、多岐にわたります。また、移動しているワークピースへの加工(オンザフライ加工)においてもガルバノスキャナ―を用いることで加工時間の短縮、高い動的性能、高精度での加工を実現します。
また、ワークピースの位置検出と次の加工のためのトラッキングも可能にします。
マイクロドリリング
微細な穴あけ加工のような難しい要件を満たすためには、それぞれの用途に特化した特別なスキャンシステムが必要となります。
回路基板や太陽電池のマイクロビア加工(メタルラップスルー、エミッタラップスルー)などの「ジャンプ&シュート」アプリケーションでは、高精度で最大のスループットを実現するスキャンシステムが必要とされます。
自由に定義された形状の注入ノズルの穴あけ加工では、高精度に製造するためのスキャンソリューションが必要です。
precSYSは、超微細な正負円錐または理想的な円柱、円形、高アスペクト比(≥10:1)の楕円形の穴の加工を可能にします。なお、一般的に要求される精度は、10μm未満の範囲です。
マイクロ彫刻
ガルバノスキャンヘッドを利用したマイクロ彫刻では、2 Dのスタンプキーやメダリオンキー溝、3 Dの鋳造型などの超微細構造の製作を可能にします。さらに、深彫り加工は数時間かかることが多いため、2D、2.5D、3Dそれぞれのスキャンシステムは、高精度と動作性を維持しながら、ドリフトの抑制が求められます。
マイクロカッティング
レーザーとガルバノスキャナーを組み合わせたスキャンシステムにより、後処理を必要とせず、狭い範囲の超微細構造を迅速かつ正確に切断できます。UPSレーザーと組み合わせることで一度に複数の加工工程を同時に実行できます。また、要求する輪郭を素早く、高い再現性でスキャンすることで素材への熱による影響はありません。
マイクロカッティングは通常、効果ガラス、ダイヤモンド、サファイヤガラス(コランダム)、ゴリラガラス、セラミック、形状記憶金属、PCB基板などに適しています。
微細加工
表面の微細加工で部品の特性を変えることができます。例えば、射出成形金型やプラスチックに電子機能、ロータス効果、滑り止め効果、皮のような表面構造を付与することが出来ます。大きな表面にこれらの構造を経済的に加工するために、レーザービームを高速かつ正確に位置決めするスキャンシステムが使用されます。ロータス効果を持つ金属やプラスチック部品、薄膜太陽電池(ロールツーロールプロセス)、ディスプレイ、スマートデバイスをコスト効率よく加工するには、非常に難しい課題をクリアしなければなりません。このような用途では、低ディザーかつ高性能のスキャンシステムが必要になります。
マイクロ波を利用した焼結
マイクロ波を利用した焼結におけるスキャンシステムでは、深彫り加工と同様に最小限のドリフト、最高の精度、高速な動作が必要です。高性能スキャンシステムは、医療技術、航空宇宙、時計製造、自動車産業で使用される高精度な金属機能部品の製造を可能にします。
微細加工における低ディザーと20ビット解像度
最高の加工結果を得るためには、レーザーとスキャンシステムの同期制御が不可欠です。スキャンシステムの高性能化に加え、位置決め制御の高解像度も必要です。一般的なXY2-100プロトコルは、16ビットの位置決め解像度しか持たないため微細加工には不十分な場合もあります。SCANLABが開発・導入した20bitのSL2-100プロトコルは理想的です。